Batteries de voitures électriques : l'enjeu des métaux critiques
La production des batteries de voitures électriques nécessite des quantités non négligeables de métaux dits « critiques », dont l’extraction a des impacts considérables sur l’environnement. L’explosion de la demande dans les années à venir va pousser la France et l’Europe à se positionner sur la production et la transformation de ces matières premières. On fait le point sur les enjeux de cette industrie.
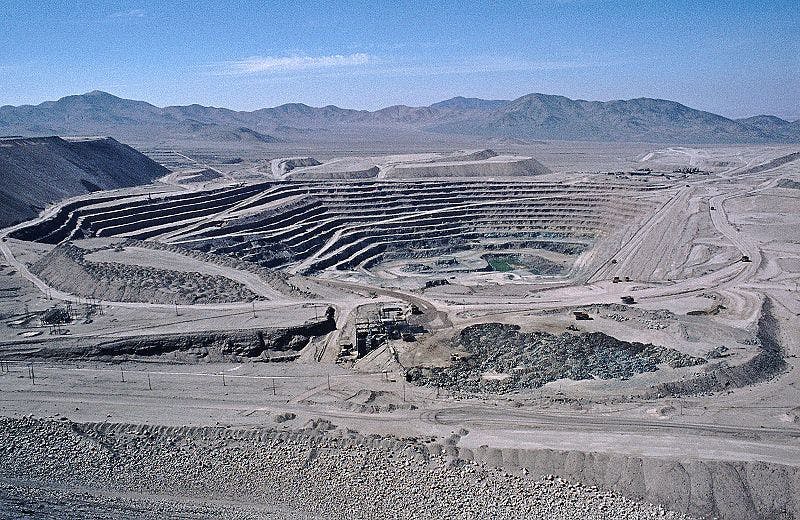
En décembre 2023, la France a atteint le million de véhicules 100% électriques en circulation. L’électrification du parc automobile français s'accélère depuis plusieurs années : d’après les chiffres publiés par AAA Data fin décembre 2023, le marché électrique a connu une croissance annuelle moyenne de 35% entre 2020 et 2022. Une tendance qui ne va faire que s’amplifier, compte tenu de l’interdiction dès 2035, de la vente de véhicules thermiques neufs. L’intensification de la production de voitures électriques neuves dans les années à venir soulève la question cruciale des ressources nécessaires. Car pour fabriquer une batterie de voiture électrique, il faut une multitude de matières premières, dont l’extraction nécessite de grandes quantités d’eau et d’énergie, ce qui a une incidence non négligeable sur l'environnement, notamment la biodiversité, et les populations. Pourtant, ce report du thermique vers l'électrique semble inévitable dans un contexte de transition énergétique… En Europe, les voitures représentent en effet 60,6% des émissions de gaz à effet de serre dues au transport routier. Et même si l'impact sur l’environnement de la production des batteries de véhicules électriques ne peut pas être réduit à néant, il existe des moyens de le minimiser…
Qu’appelle-t-on « métaux critiques » ?
Pour bien comprendre les enjeux de cette industrie, il faut commencer par définir ce qu’est un métal critique. Sur son portail « Vie Publique », le gouvernement rappelle qu’il s’agit de matières premières « pour lesquelles un risque pèse sur la chaîne d’approvisionnement, soit parce que celle-ci est concentrée dans un très petit nombre de pays, soit parce que la stabilité politique des pays fournisseurs est limitée ». Pour la Commission européenne, les matières sont considérées critiques « lorsqu’elles revêtent une importance économique cruciale mais qu’elles ne peuvent être produites de manière fiable dans l’Union européenne et qu’elles doivent donc être en grande partie importées ». En résumé, ces métaux sont donc dits « critiques » car il existe une tension au niveau de leur capacité d’approvisionnement. L’Union européenne a listé 34 matières premières critiques en 2023, parmi lesquelles on trouve des métaux tels que le cobalt, le cuivre, le manganèse, le lithium, le nickel, le magnésium, ou encore le tungstène, ainsi que des matières premières minérales telles que la bauxite (minerai à partir duquel on produit l’aluminium), ou le graphite.
Souvent, on entend parler de « terres rares » pour la production de batteries de voitures électriques, mais il s’agit d’une erreur : il ne faut pas confondre « métaux critiques » et « terres rares ». Les terres rares sont un sous-ensemble de matériaux critiques, mais tous les matériaux critiques ne sont pas des terres rares ! 17 éléments sont considérés comme « terres rares », dont le scandium, le cérium, le terbium ou le thulium… Des noms barbares qui définissent des métaux (et non des terres) qui ne sont pas si rares, contrairement à ce que leur nom suggère. Leurs réserves sont en effet assez importantes et réparties sur les cinq continents. Et surtout : aucune terre rare n’entre dans la composition d’une batterie lithium-ion.
Bon à savoir
Quand on parle de « métaux critiques », il n’est pas rare de voir l’emploi des termes « matériaux critiques ». Les deux sont justes, car les métaux sont un type de matériau. Mais il est donc plus précis d’employer les termes « métaux critiques » quand il s’agit de matériaux métalliques. Certains matériaux critiques qui entrent dans la fabrication des batteries de voitures électriques ne sont pas des métaux !
Quels sont les métaux critiques utilisés pour la fabrication des batteries lithium-ion ?
Une batterie de voiture électrique est « un accumulateur qui transforme de l’énergie chimique en énergie électrique. L’énergie chimique est transformée en énergie électrique lors des phases de décharge et une petite partie en chaleur », explique l’association Avere-France. Une batterie est composée de cellules et chaque cellule est elle-même composée d’une cathode, d’une anode, d’un séparateur et d’un électrolyte.
Bon à savoir
L’anode et la cathode sont les points d’entrée et de sortie du courant. Sur une batterie de voiture électrique « Les cathodes et anodes (…) sont alternativement positives et négatives selon leur état, charge ou décharge », précise l’Avere-France.
L'anode est généralement composée de graphite ; quant à la cathode, elle est composée de divers éléments chimiques qui diffèrent selon la technologie de la batterie. La plus courante est la technologie NMC, à base de lithium, nickel, manganèse et cobalt. Mais il existe aussi des batteries NCA (lithium, nickel, cobalt et aluminium) et LFP (lithium, phosphate de fer). Ces accumulateurs sont donc composés de métaux critiques, que l'on retrouve aussi dans le bloc-moteur (où du cuivre est également nécessaire) et dans la carrosserie. D’après les chiffres publiés dans une étude du WWF France avec l’Institut du développement durable et des relations internationales (IDDRI), la fabrication d’un véhicule électrique nécessite environ 394 kg de matériaux critiques : aluminium, cobalt, cuivre, graphite, lithium, manganèse et nickel en majorité. C’est 2,2 fois plus que pour la fabrication d’une voiture thermique, qui en nécessite 176 kg (aluminium, cuivre et manganèse).
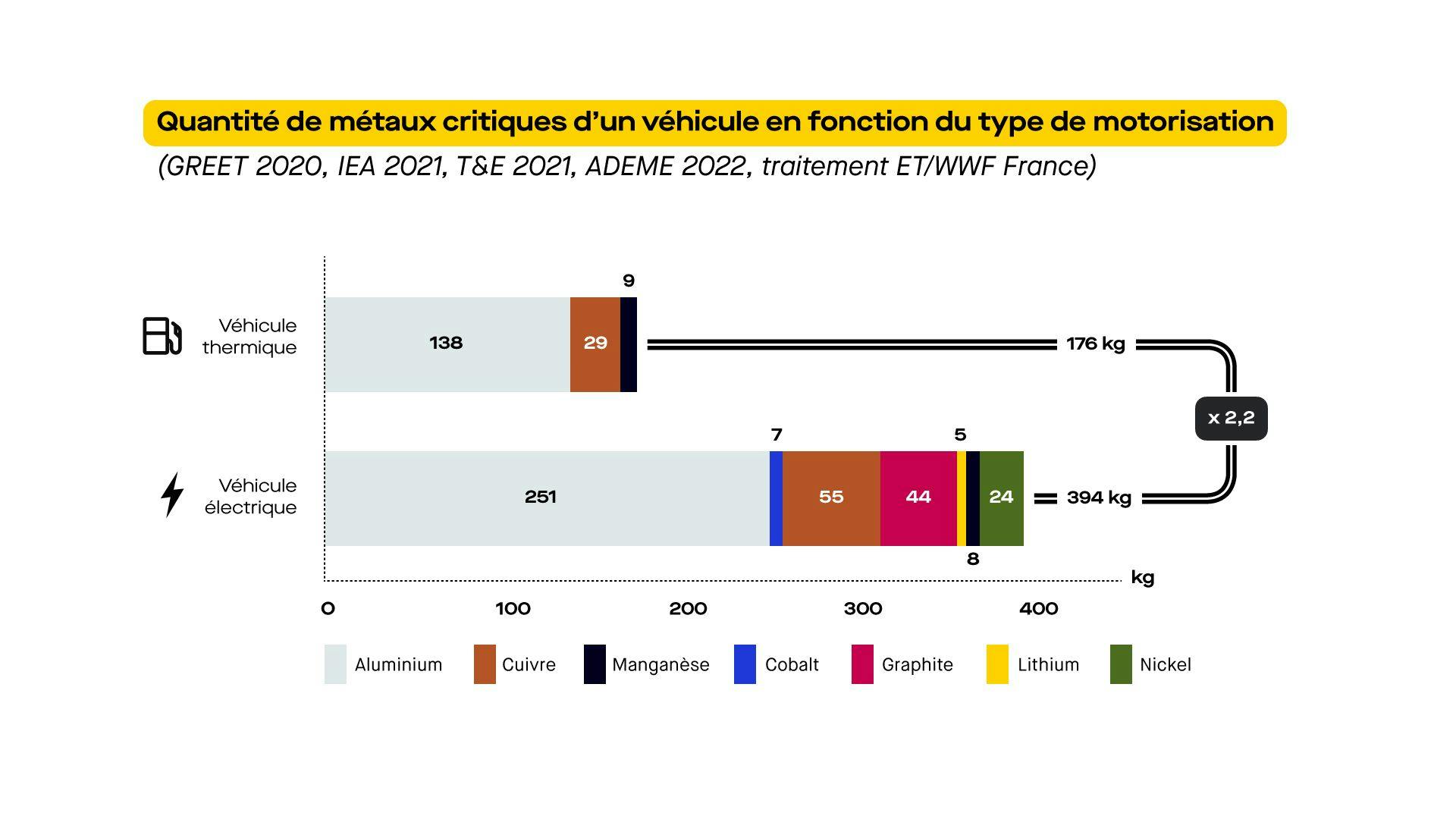
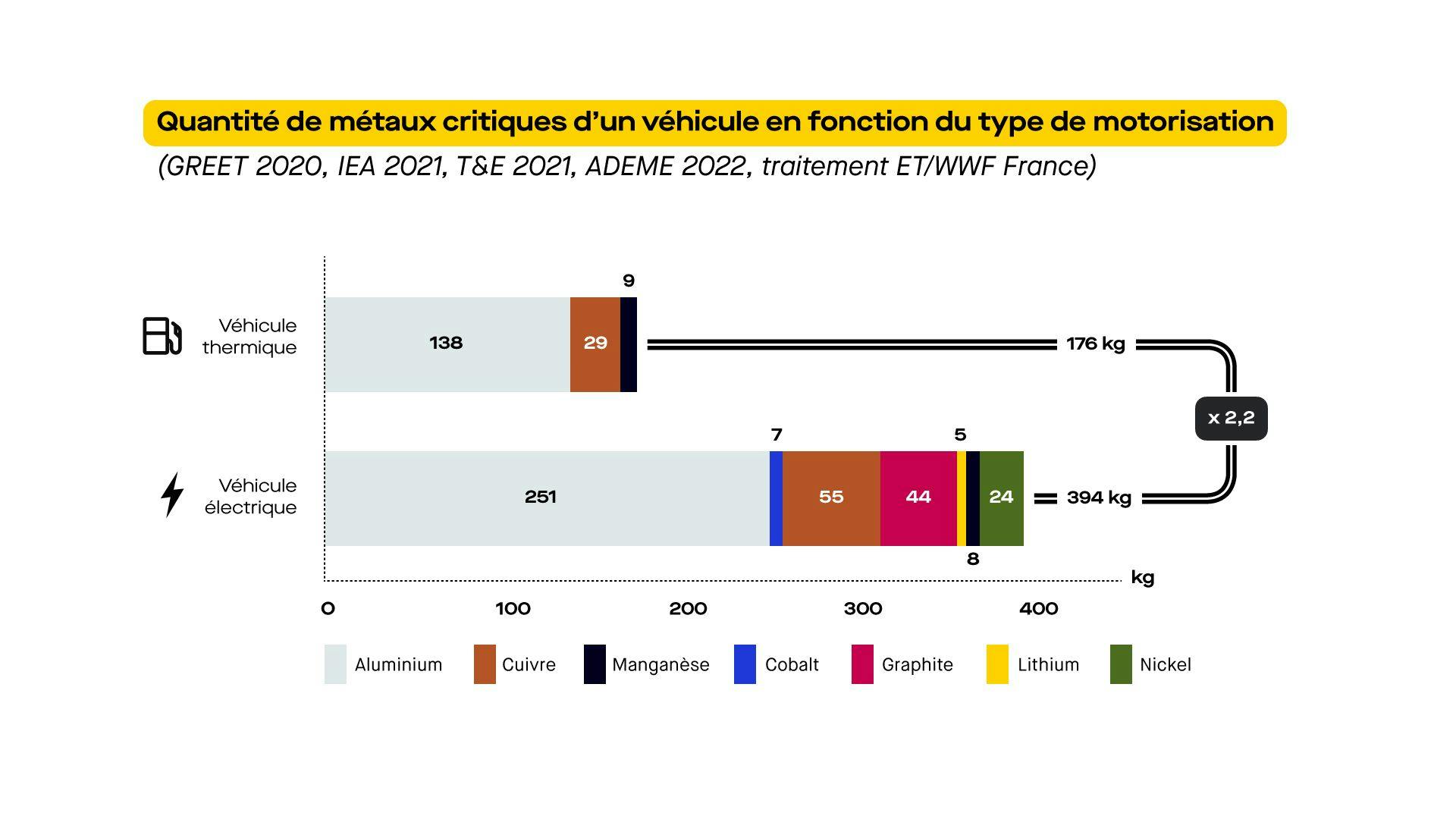
L’industrie automobile n’est par ailleurs pas la seule à utiliser des métaux critiques : on en trouve dans de nombreux objets du quotidien : le cuivre dans les plomberies et les fils téléphoniques, le nickel dans les appareils électroménagers, ou encore l’aluminium (produit à partir de la bauxite, considérée comme matière première critique), qui est le métal le plus utilisé après le fer.
Le défi de l’approvisionnement
Dans le cadre de la transition écologique, « la voiture électrique occupe la première place de la demande en matières premières critiques, avec plus de 50% du volume en 2040, dans un scénario limitant le réchauffement à 2°C », souligne l’étude du WWF et de l’IDDRI. Le souci, c’est que les capacités de production actuelles vont vite être dépassées par la demande, qui croît très rapidement. « Les besoins vont exploser », confirme Jean-Philippe Hermine, directeur de l’Institut mobilité en transition de l’IDDRI dans le podcast « Les matériaux critiques dans les batteries : quel est vraiment l’enjeu ? ». « On va avoir besoin de vingt fois plus de batteries d’ici 2040 et ce qu’on sait déjà, c’est qu’on va devoir multiplier par sept les quantités de lithium qu’on va consommer d’ici 2030, et par deux les quantités de cobalt et de nickel », ajoute-t-il. Olivier Vidal, géologue et directeur de recherche au CNRS estime même que « la quantité cumulée de métaux à produire au cours des 35 prochaines années dépasserait la quantité cumulée produite depuis l’antiquité* ».
Autre problème de taille : l’extraction et le raffinage de ces métaux est concentrée dans une poignée de pays, dont aucun n’est situé en Europe. 70% du cobalt provient de République démocratique du Congo, 45% du nickel provient d’Indonésie, 50% du lithium est extrait en Australie et 26% au Chili, pays qui domine également l’extraction du cuivre**. La transformation de ces métaux est quant à elle en grande majorité réalisée en Chine : le pays « produit plus de 50% du marché du raffinage et de la transformation de ces matériaux et plus de 80% du marché des anodes, des cathodes, des électrolytes et des cellules de batteries », souligne l’étude du WWF et de l’IDDRI. De fait, les pays européens seraient dépendants à environ 80% du reste du monde pour la production et la transformation de ces métaux indispensables à la fabrication des batteries. Et ces tensions ont des répercussions sur les prix des métaux, ainsi que sur le prix du produit final : la batterie. Entre janvier 2021 et mars 2022, le prix du cobalt a augmenté de 150% et celui du lithium de 740%. « L’IEA [Agence internationale de l’énergie, Ndlr] estime qu’une augmentation de 10 % du prix des métaux suivants : lithium, nickel et cobalt, entraîne une hausse du prix du pack de batteries de 3 % pour les batteries NMC les plus répandues », rappelle le WWF dans son rapport.
Quel impact sur l’environnement ?
Au-delà des tensions d’approvisionnement, l’extraction et la transformation de ces métaux a des répercussions importantes sur l’environnement. « Les conditions de production de ces matières premières ont un impact, d’un point de vue social et environnemental », confirme Jean-Philippe Hermine. « Aucune mine n’est réellement propre, mais il y a des mines qui sont plus ou moins sales. Certaines utilisent moins d’eau et la recyclent, ainsi que de l’énergie décarbonée. Il y a donc une grosse graduation d’impact entre les différentes mines. Il est très important d’être vigilant sur ce point », ajoute-t-il. A titre d’exemple, au Chili, « les deux sociétés minières exploitant du lithium dans la zone d’Atacama, ainsi que deux sociétés minières de cuivre proches, représentent ensemble un volume d’extraction de 4 230 litres d'eau douce par seconde », expose l’association négaWatt dans sa note d’analyse « Lithium : vers une indispensable sobriété ». « Au niveau national, en 2016, les autorités chiliennes considéraient que 70 % de l'eau du pays était utilisée pour les opérations minières et 17 % pour le secteur agricole, ne laissant que 13 % pour la consommation humaine », est-il précisé.
Quel avenir pour la production de batteries en Europe ?
Construire une filière plus respectueuse de l'environnement est d’ailleurs l’un des enjeux de l’Europe dans sa recherche d’indépendance : il s’agit de créer des mines exploitées de la façon la plus durable possible, ainsi qu’une chaîne de raffinage qui permettrait de sortir progressivement de la dépendance à la Chine. « C’est possible et c’est indispensable », considère Jean-Philippe Hermine. « C’est d’ailleurs l’objet des politiques actuelles développées au niveau européen et national sur l’industrie [Plan Industrie verte en France et Pacte Green Deal en Europe, Ndlr]. Il est très important de développer ces savoir-faire, au-delà des gigafactories qui ne font que l’assemblage des batteries, et au-delà de l’ouverture des mines », poursuit-il.
Bon à savoir
L’Europe a pour ambition de transformer sur son territoire au moins 40 % de sa consommation annuelle en matières premières stratégiques d’ici 2030. Les matières premières sont dites « stratégiques » quand elles sont localisées dans le monde de façon inéquitable, ou bien qu’elles sont difficilement accessibles ou très coûteuses, tout en étant indispensables pour l’activité industrielle, les technologies ou la sécurité. Les métaux critiques utilisés dans la fabrication des batteries figurent également dans la liste européenne des métaux stratégiques.
En théorie, relocaliser l’extraction et la transformation de ces métaux en Europe est réalisable. Mais cela ne se fera pas en un clin d’œil : il faut en effet compter jusqu’à une dizaine d’années pour lancer l’exploitation d’une mine. « Produire du nickel propre peut se faire en Europe, comme en Finlande, mais c’est plus cher. Les mines de cuivre sont longues et coûteuses à construire et la qualité des ressources tend à diminuer (…) et le graphite est peu abondant et largement contrôlé par la Chine », souligne le rapport de l’Institut français des relations internationales (IFRI), « Comment gagner le pari industriel de la mobilité électrique en France ? ». Selon l’IFRI, l’Europe doit travailler en priorité à l’amélioration de l’empreinte environnementale de l’extraction du lithium, dont il existe des gisements en France – notamment dans l’Allier –, à l’extraction et au recyclage du cuivre, à la transformation du nickel propre et sur la chaîne de valeur du graphite. « Dernier enjeu majeur : la production d’aluminium bas-carbone, pour laquelle un pays avec un parc nucléaire comme la France est particulièrement bien positionné », souligne l’Institut.
L'IFRI a d'ailleurs réalisé une carte qui regroupe tous les projets industriels en cours et annoncés à horizon 2030 sur le territoire français (voir ci-dessous). Des projets qui représentent tous les maillons de la chaîne de production des véhicules électriques.
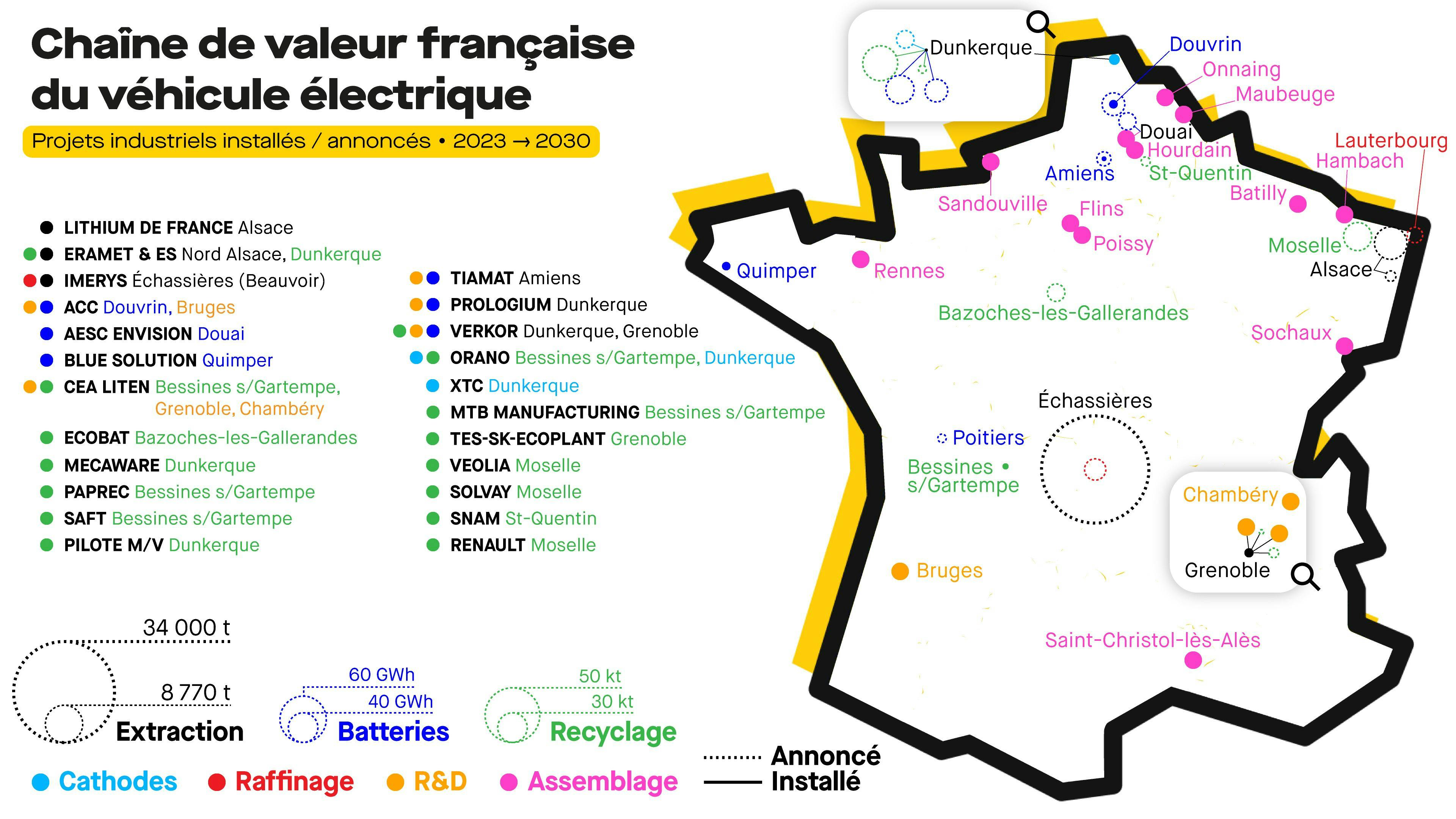
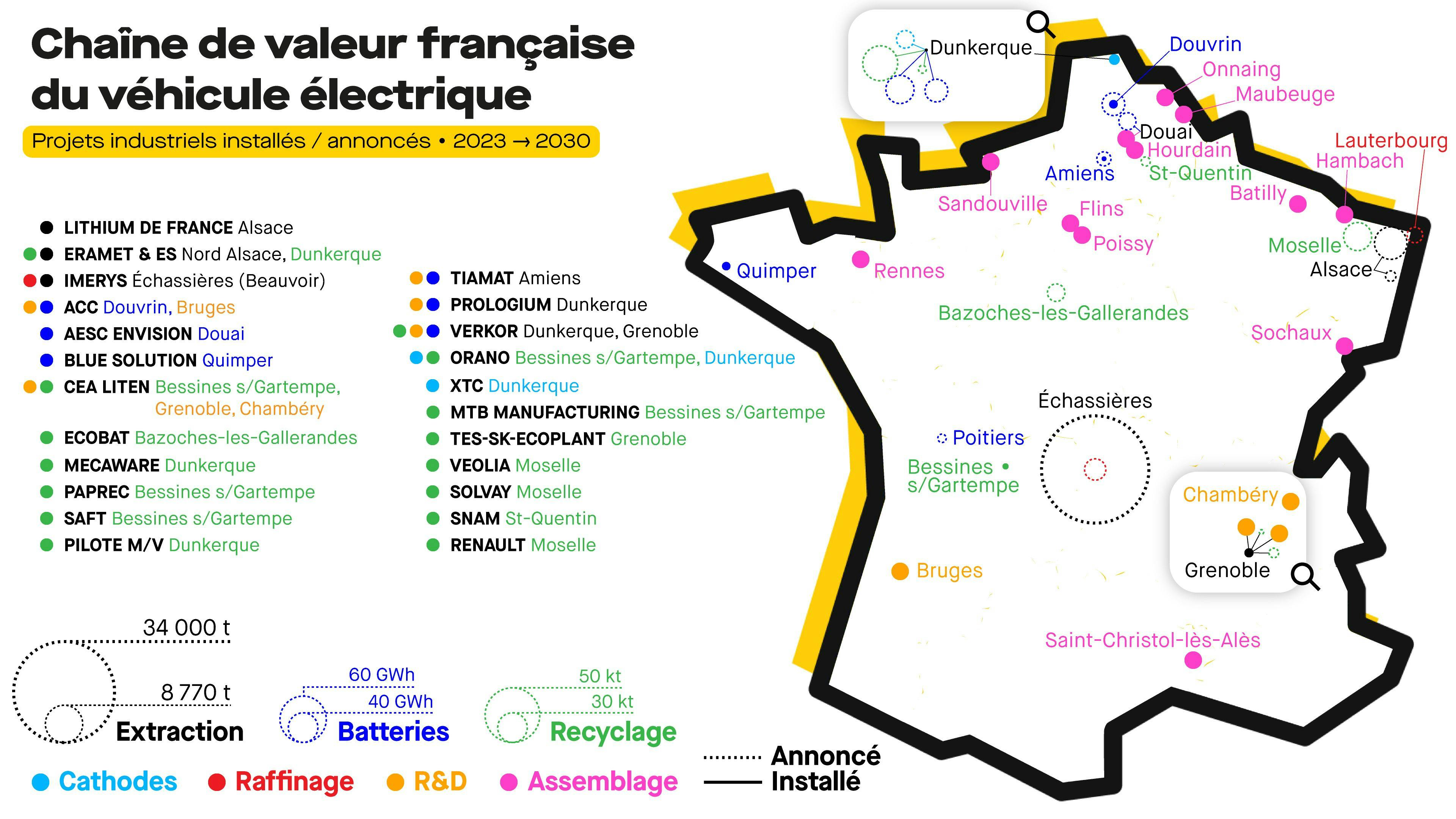
Bon à savoir
Le Bureau de recherches géologiques et minières (BRGM) a réalisé un atlas des substances minières présentes en France métropolitaine, parmi lesquelles on trouve le cuivre, le lithium, le cobalt ou encore le nickel, tous nécessaires à la production de batteries de voitures électriques.
Diminuer la taille des voitures : un levier clé pour limiter les besoins en métaux
Mais d’autres paramètres extérieurs à la chaîne de production des batteries entrent en jeu dans cette course à l’indépendance… L’IFRI et le WWF sont d’accord sur ce point : il s’agit de repenser nos mobilités et de réduire la taille des voitures (et donc celle des batteries) pour réduire la demande en métaux critiques. D’après le rapport WWF/IDDRI, la France a un potentiel de production annuelle de 16 kilotonnes de lithium dès 2030. Dans son scénario le plus optimiste – qui implique la mise en œuvre de politiques publiques volontaristes pour sortir de la dépendance à la voiture individuelle – la France couvre ses besoins en lithium et peut même exporter 20 kilotonnes excédentaires (sur la période 2030-2040), soit la quantité nécessaire pour équiper 230 000 voitures électriques de batteries de 50 kWh.
Un SUV électrique consomme 3 fois plus de cuivre et d’aluminium, et 5 fois plus de lithium, de nickel, de cobalt, de manganèse et de graphite qu’une citadine électrique.
Rapport WWF/IDDRI/EY
La réduction de la taille des véhicules semble être un levier relativement simple à appliquer, avec des impacts concrets : un SUV électrique consomme en effet trois fois plus de cuivre, trois fois plus d’aluminium, cinq fois plus de lithium, cinq fois plus de nickel, cinq fois plus de cobalt, cinq fois plus de manganèse et cinq fois plus de graphite qu’une citadine électrique. Même avec tous ces efforts, il faudra continuer à importer certains métaux, mais la dépendance pourrait se réduire très significativement.
Le recyclage : maillon essentiel de la chaîne
Une fois que l’Europe aura réussi à créer sa chaîne de production et de transformation des métaux, ainsi que d’assemblage des batteries, le dernier maillon de la chaîne – et pas des moindres – sera déterminant : le recyclage des batteries et la réutilisation des métaux critiques est crucial pour contribuer à réduire la dépendance des pays européens aux pays producteurs. « En 2019, les entreprises françaises de recyclage étaient capables de recycler 5 000 tonnes de batterie par an, et l’ensemble des acteurs européens entre 15 000 et 20 000 tonnes. D‘ici à 2027, il faudra que l’Europe multiplie sa capacité de traitement par trois », écrit l’Agence de la transition écologique (Ademe) dans son avis, « Voitures électriques et bornes de recharge ». L’ambition de l’Union européenne à date est d’atteindre un taux de récupération de 90% pour le nickel, le cobalt et le cuivre et de 35% pour le lithium. Pour l’instant, on estime que seuls 5 à 7% des batteries lithium-ion sont recyclées dans le monde, dont la moitié sont traitées en Chine***.
Une réduction graduelle des besoins en métaux
Mais le recyclage ne pourra être une source d’approvisionnement prometteuse qu’à partir de 2040, quand les batteries utilisées actuellement arriveront en fin de vie. « Néanmoins, cette perspective d’une économie circulaire dans le secteur des batteries doit être préparée et engagée dès à présent pour être au rendez-vous, en s’appuyant notamment sur les premiers déchets d’usinage produits par les gigafactories qui s’installent partout en Europe », considère le WWF dans son rapport. Le recyclage des batteries pourrait ainsi permettre de couvrir 16% des besoins cumulés en lithium entre 2022 et 2050, 20% des besoins cumulés en nickel et 28% des besoins cumulés en cobalt. « Au final, le recyclage permettra de réduire en moyenne de 11 % le besoin cumulé en lithium, en nickel et en cobalt à extraire entre 2022 et 2035, puis de 29 % sur la période 2035 et 2050 pour assurer l’électrification du parc automobile », estime le WWF. Pour l’IFRI – dans un scénario de sobriété impliquant une diminution de 15 % du parc automobile et une taille moyenne des batteries limitée à 40 kWh – grâce au recyclage, « la réduction des besoins [serait] de 38 % pour toutes les matières premières ».
Bon à savoir
Quand une batterie n’a plus la puissance nécessaire pour propulser une voiture électrique, elle peut avoir une seconde vie lors de laquelle elle est utilisée pour un stockage stationnaire d’énergie. Cette énergie stockée – souvent de l’électricité renouvelable produite par des panneaux solaires ou des éoliennes – est ensuite réutilisée ou réinjectée dans le réseau électrique.
« En complémentarité du potentiel de l’économie circulaire et du recyclage dans le besoin en métaux critiques, les avancées technologiques en matière de composition chimique des batteries sont appelées à tenir un rôle conséquent dans la réduction, à terme, des matières premières critiques », relève le rapport du WWF. D’après BloombergNEF, le mix mondial de chimies de batterie évoluera en 2035 vers des chimies de batteries de type NMC plus intenses en nickel et moins gourmandes en cobalt. « La diversification des chimies permettrait de réduire de manière considérable le besoin en cobalt, nickel et manganèse, à hauteur de 30 % », estime par ailleurs l’IFRI dans son scénario le plus optimiste.
Sobriété et réduction de la demande
Les tensions sur l’approvisionnement en métaux critiques sont donc une réalité, mais elles pourraient n’être que temporaires, à condition que l’extraction, la transformation et le recyclage des métaux critiques nécessaires à la production des batteries soient largement réimplantées en France et en Europe. Mais il faudra inévitablement que les pays européens se posent des questions sur leurs besoins en mobilité. « Il faut qu’on aille vers des véhicules plus petits, avec des batteries plus petites, moins se déplacer, ou partager les véhicules… Donc on en revient de toute façon à la question de la sobriété et de la réduction de la demande. C’est non seulement vertueux, mais ça s’impose d’un point de vue industriel par rapport à cet enjeu minier des matériaux critiques », conclut Jean-Philippe Hermine.
*** Chiffres : note d’analyse de négaWatt – Lithium : vers une indispensable sobriété (février 2023)
Photo d'ouverture : Mine de cuivre de Chuquicamata au Chili, en 2007, I, 天然ガス, CC BY-SA 4.0 via Wikimedia Commons